Abbiamo scelto di parlare di digitalizzazione dando voce direttamente ad un imprenditore che ha puntato sull’innovazione digitale per supportare il processo di crescita della propria azienda.
Luca Mauri, Managing Director di F.lli Mauri SpA, azienda leader nel settore fasteners che produce e commercializza a livello internazionale soluzioni di fissaggio di alta qualità, ha iniziato il suo percorso di digitalizzazione con jpiano® accompagnato da AEC Soluzioni nel 2017.
Gli abbiamo posto alcune domande per comprendere quali siano stati gli effetti concreti dell’introduzione di un sistema MES evoluto per il monitoraggio e controllo delle attività della fabbrica.
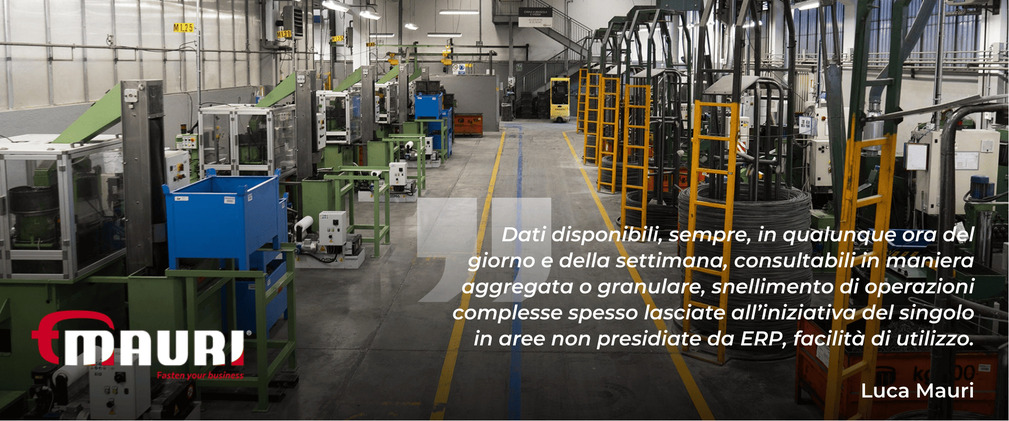
Qual è stato il bisogno principale che ha dato avvio al processo di digitalizzazione 4.0 in F.lli Mauri?
Il mondo IT mi ha sempre interessato fin da giovane, ricordo che da bambino mi divertivo a smontare i pc per vedere cosa contenevano, con grande gioia di chi me li aveva regalati, quindi curiosità è la prima mia caratteristica per tutto quello che riguarda la tecnologia.
Il processo di digitalizzazione in Mauri era programmato da tempo, infatti vi era esigenza di avere i dati in tempo reale perché da alcuni anni utilizzavo per analisi la BI e la sete di informazioni era vitale, giocoforza il collegamento ad un MES era un passaggio obbligato.
Sulla base di quali elementi ha scelto di avvalersi di AEC Soluzioni e di utilizzare jpiano® come strumento centrale per la digitalizzazione in azienda?
Ricordo di avere conosciuto i titolari Antonio e Davide durante una visita presso la fiera A&T Lingotto, e sono rimasto affascinato dal modo con cui descrivevano il loro prodotto, si vedeva che non erano venditori ma tecnici, quindi, con sicuramente da parte mia presunzione di successo, ho deciso di sceglierli come partner per il processo di digitalizzazione della fabbrica.
Quanto è stato facile (o difficile) implementare il sistema jpiano® all’interno di un processo già consolidato?
Nel mio percorso lavorativo ho sperimentato che non esiste nulla di semplice, occorre semplicemente non arrendersi mai, ma soprattutto avere le persone giuste dalla tua parte. Ho modellizzato il mio primo ERP a vent’anni e oggi che vado per i sessanta mi sto divertendo a modellizzare il secondo ERP unitamente a far crescere, tenendolo per mano, il MES.
Jpiano® non è difficile e non è facile, dipende dalla maturità digitale dell’azienda e da quanto tempo/ risorse intendi dedicare ad esso, inserirlo in un processo consolidato non è un grosso problema anche perché sono gli stessi operatori, appena si accorgono delle potenzialità del MES, a dare spinta per avere sempre maggiori funzioni integrate e accessibili.
L’integrazione del sistema MES jpiano® con altri software, specialmente quelli sviluppati internamente, ha presentato ostacoli? e in tal caso come sono stati superati?
I database interfacciati non sono più un problema, c’è da fare un attento lavoro di analisi per non dimenticarsi dei campi importanti, ma sia software licenziati che fatti in casa dialogano tranquillamente con jpiano®, oltretutto Davide ha competenze introvabili in termini di interfacce.
In azienda abbiamo un insieme di 11 DATABASE sincronizzati con due ERP in fase di passaggio, quindi può immaginare la mole di connettori da tenere attivi.
Ostacoli ce ne sono stati, ma lavori di brainstorming hanno permesso di superarli brillantemente.
Durante gli ultimi sette anni, come si è evoluta la vostra azienda? In che modo jpiano® ha accompagnato questa crescita?
Il MES jpiano® è partito in sordina, andando a connettere le funzioni principali della macchina, come acceso/spento/produce eccetera, quindi all’inizio è stata easy, poi abbiamo alzato l’asticella con il progetto MM8, un progetto sviluppato a partire dal 2019 con l’appoggio di fondi EU Por-FESR, dove abbiamo sviluppato internamente la parte HMI della macchina integrandola a profondo livello con jpiano® sia in ingresso che uscita ricetta.
Devo dire che dopo questa esperienza strong il resto è venuto da sé, oggi sul centinaio di macchine presenti in azienda (con età molto variabile) sono arrivato a circa 80% della copertura da parte di jpiano®.
L’ultimo progetto denominato AFP, di cui sono particolarmente orgoglioso essendo stata una delle prime Midcap italiane ad averlo assegnato da parte del MiSE, è riuscito ad essere finanziato mediante i fondi REACT EU anche grazie alla profonda integrazione tra MES-ERP-BI.
Direi che in sette anni ne abbiamo fatte di cose, che ne pensa?
Quali sono i principali benefici che ha riscontrato?
Dati disponibili, sempre, in qualunque ora del giorno e della settimana, consultabili mediante BI in maniera aggregata o granulare, snellimento di operazioni complesse spesso lasciate all’iniziativa del singolo in aree non presidiate da ERP, facilità di utilizzo.
Sorrido quando ricordo di aver testato gratuitamente la connessione wi-fi su uno dei miei frequenti voli intercontinentali, ricordo che ero curioso di vedere le MM8 funzionare e dal cielo mi sono collegato alle macchine mediante smartphone via jpiano® Web.
Ci può raccontare un caso in cui grazie a jpiano® è riuscito a risolvere un problema importante?
Direi sicuramente le dichiarazioni di cambio utensile legate all’operatore dove non avevamo un presidio in quanto zona non attenzionata da ERP, con alert di superamento soglie, in notifica automatico ai responsabili di reparto per interventi urgenti. Questa è un’area dove ho ottenuto veramente un presidio delle informazioni che altrimenti sarebbero disperse.
In che modo jpiano® ha migliorato la qualità del lavoro dei suoi dipendenti?
Torniamo alla disponibilità di informazioni complesse in tempo reale: questo vale per me come CEO come sintesi, ma vale per gli operatori come dato granulare. Solo avendo l’informazione quando voglio ottengo risultati, jpiano® va inteso anche in questo senso, un aiuto all’operatore che non si deve prendere appunti su un taccuino per ricordarsi cosa ha fatto come regolazione alla macchina per vedere che adesso va bene.
La sua azienda è nota per l’attenzione all’ambiente. In termini di sostenibilità che contributo può dare un software come jpiano?
Il mio personale percorso verso obiettivi ESG mi porta ogni volta a ragionare per prendere scelte consapevoli che premiamo non solo aspetti legati alla produttività ma soprattutto all’efficientamento energetico, e qui jpiano® aiuta notevolmente in quanto permette un’attenta calibrazione dei parametri macchina e quindi del risparmio ottenibile a parità di resa.
In quattro anni abbiamo ottenuto tre certificazioni ISO, tra cui la ISO 28000 anche qui primi in Italia ad ottenerla, sono state scelte consapevoli che hanno permesso all’azienda di maturare ed essere pronta alla dichiarazione ambientale di prossima pubblicazione con largo anticipo sulle normative EU.
Che consiglio darebbe ad altre aziende del settore che stanno valutando l’adozione di un software MES per il controllo della produzione?
Di fare un’attenta analisi dentro di sé per prima cosa, e trovare uno speed entusiastic manager o team, che provi reale passione nel prendere un bambino e portarlo per mano per farlo crescere e correre sempre più veloce ed integrato.
Da una parte quindi conoscenza dei propri processi IT e dall’altra voglia di rischiare e azzardo per inserire processi innovativi che vanno spesso rodati affinché raggiungano il desiderata.
Nel mondo della programmazione non esiste nulla che funziona al primo colpo, ma questo è il bello.